Recognizing What is Porosity in Welding: Causes and Solutions
Wiki Article
Porosity in Welding: Identifying Common Issues and Implementing Finest Practices for Avoidance
Porosity in welding is a prevalent concern that often goes unnoticed until it causes significant problems with the integrity of welds. This common problem can jeopardize the stamina and toughness of bonded frameworks, presenting safety and security threats and causing pricey rework. By recognizing the origin creates of porosity and applying reliable prevention strategies, welders can dramatically enhance the quality and integrity of their welds. In this discussion, we will certainly check out the key variables adding to porosity development, analyze its damaging impacts on weld performance, and discuss the very best practices that can be taken on to reduce porosity event in welding processes.Common Root Causes Of Porosity
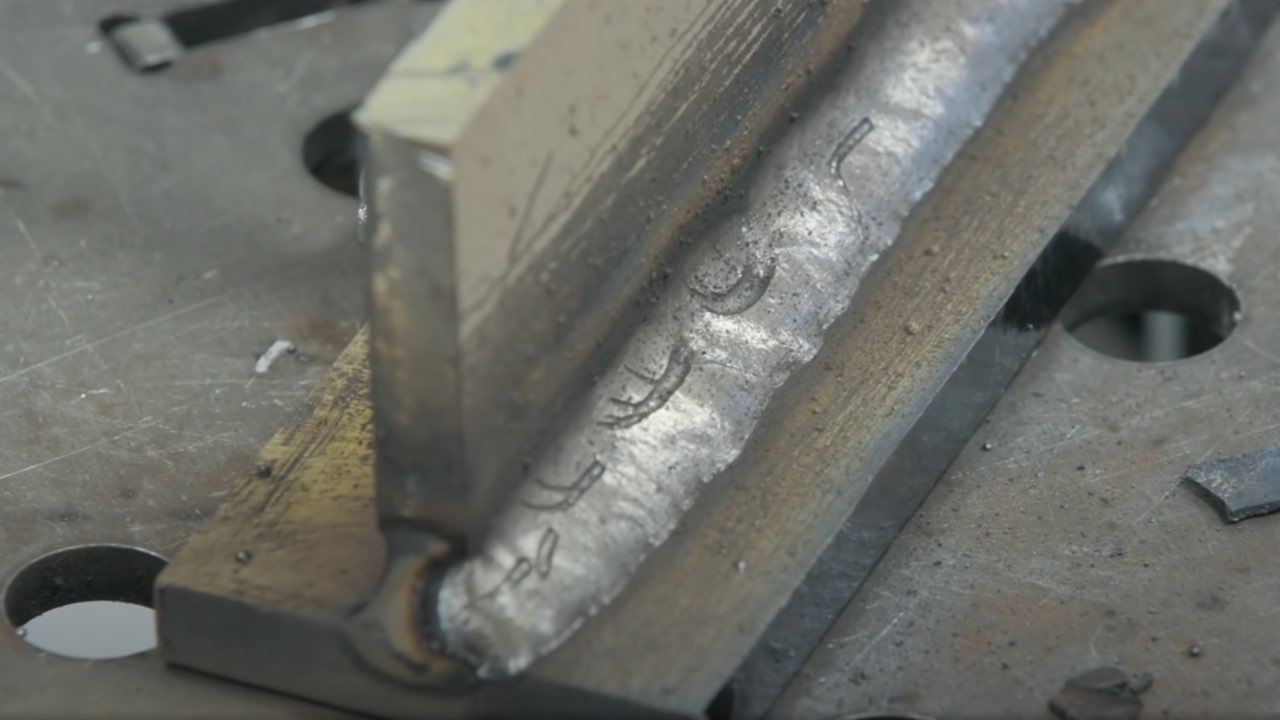
One more regular perpetrator behind porosity is the visibility of impurities on the surface area of the base steel, such as oil, oil, or corrosion. When these pollutants are not successfully gotten rid of before welding, they can vaporize and become entraped in the weld, causing flaws. Utilizing dirty or wet filler products can present pollutants right into the weld, contributing to porosity issues. To mitigate these usual sources of porosity, extensive cleansing of base steels, correct securing gas selection, and adherence to optimal welding parameters are vital methods in attaining high-grade, porosity-free welds.
Influence of Porosity on Weld High Quality

The presence of porosity in welding can substantially jeopardize the structural integrity and mechanical properties of bonded joints. Porosity develops spaces within the weld metal, weakening its total stamina and load-bearing capability. These voids work as stress and anxiety focus points, making the weld more at risk to splitting and failure under applied lots. Furthermore, porosity can reduce the weld's resistance to deterioration and various other environmental variables, additionally decreasing its longevity and efficiency.
One of the key effects of porosity is a decrease in the weld's ductility and strength. Welds with high porosity degrees tend to show reduced impact strength and decreased capability to flaw plastically before fracturing. This can be especially concerning in applications where the bonded elements go through vibrant or cyclic loading conditions. Moreover, porosity can their explanation impede the weld's capability to effectively transfer pressures, leading to premature weld failing and potential security threats in crucial frameworks.
Finest Practices for Porosity Avoidance
To enhance the architectural stability and top quality of bonded joints, what specific actions can be executed to minimize the incident of porosity during the welding procedure? Using the right welding strategy for the details product being welded, such as adjusting the welding angle and gun setting, can additionally protect against porosity. Routine inspection of welds and prompt remediation of any type of concerns determined throughout the welding process are necessary practices to stop porosity and produce top notch welds.Importance of Appropriate Welding Strategies
Executing appropriate welding strategies is critical in making sure the structural integrity and high quality of bonded joints, look at this site building on the foundation of reliable porosity avoidance measures. Welding methods straight influence the overall strength and toughness of the bonded structure. One vital facet of appropriate welding techniques is maintaining the proper heat input. Excessive warm can cause raised porosity as a result of the entrapment of gases in the weld pool. Conversely, inadequate warm may lead to insufficient blend, developing possible powerlessness in the joint. Additionally, making use of the proper welding specifications, such as voltage, current, and take a trip speed, is critical for attaining audio welds with marginal porosity.Moreover, the choice of welding process, whether it be MIG, TIG, or stick welding, need to align with the certain requirements of the job to ensure optimum outcomes. Appropriate cleaning and prep work of the base metal, as well as picking the ideal filler material, are additionally necessary elements of competent welding strategies. By adhering to these my site ideal techniques, welders can reduce the danger of porosity development and generate high-quality, structurally sound welds.
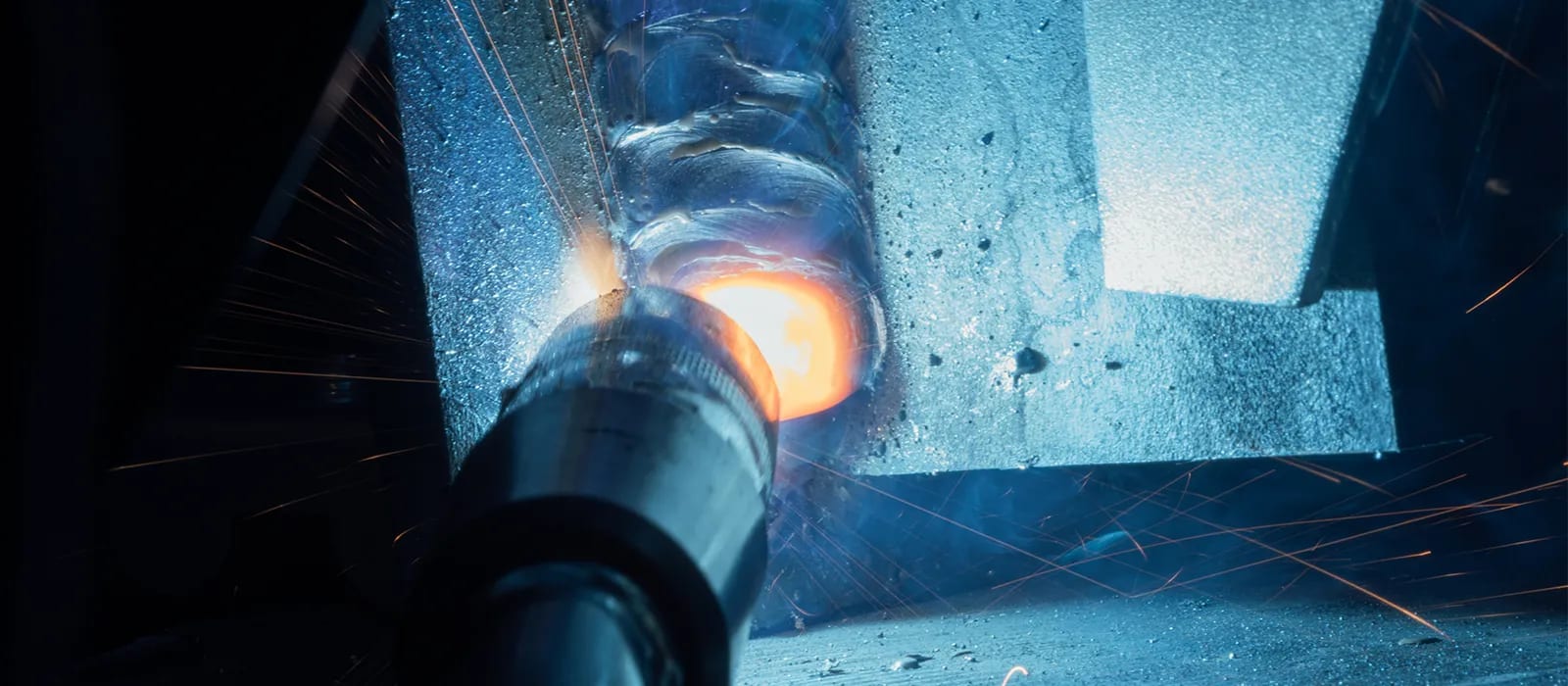
Testing and High Quality Control Actions
Examining treatments are essential to detect and prevent porosity in welding, guaranteeing the strength and durability of the last item. Non-destructive screening techniques such as ultrasonic screening, radiographic testing, and aesthetic examination are generally used to identify potential defects like porosity.Conducting pre-weld and post-weld evaluations is also vital in maintaining quality assurance requirements. Pre-weld assessments include confirming the products, devices setups, and sanitation of the work location to avoid contamination. Post-weld inspections, on the other hand, evaluate the final weld for any type of flaws, consisting of porosity, and verify that it satisfies specified requirements. Carrying out a detailed quality assurance strategy that includes complete screening procedures and inspections is extremely important to decreasing porosity concerns and guaranteeing the total high quality of welded joints.
Conclusion
To conclude, porosity in welding can be a typical issue that influences the high quality of welds. By identifying the usual sources of porosity and implementing ideal methods for avoidance, such as appropriate welding techniques and screening steps, welders can make certain top quality and dependable welds. It is vital to prioritize avoidance techniques to decrease the incident of porosity and maintain the stability of bonded structures.Report this wiki page